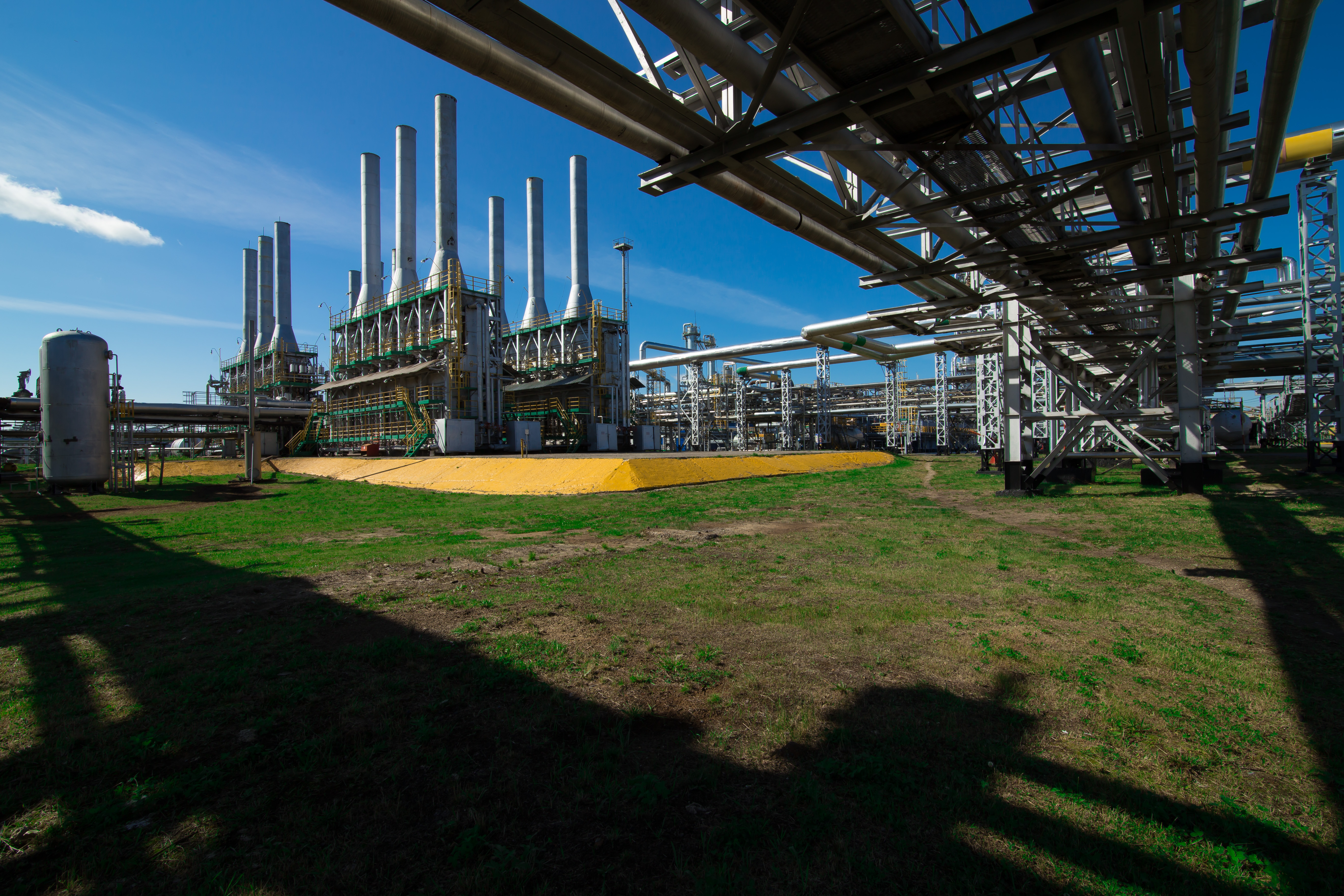
Q: When was synthetic rubber first developed?
A: In 1826, Michael Faraday defined the molecular structure of natural rubber, while in 1860 Greville Williams was able to use natural rubber to distil a spirit, which he called ‘isoprene’. However, it was not until the early 20th century, when the demand for rubber exceeded supply, causing prices to rise, that the first steps were taken to synthesise an alternative material: in 1909, Fritz Hofmann succeeded in polymerizing methyl isoprene, the first synthetic rubber, in Germany; meanwhile Kondakov, a Russian chemist, found that dimethylbutadiene could be converted into an elastic polymer. However, it was in 1910 that the commercial production of synthetic rubber became feasible, when the discovery was made independently by two Englishmen, Matthews and Strange, and a German, Harries, that sodium could be used as a catalyst to speed up polymerization. During the war of 1914-1918, methyl rubber was made in Germany on a commercial scale.
Q: How is synthetic rubber produced today?
A: There are over 200 types of synthetic rubber, each having its own constituents and qualities. However, all involve the polymerization process, which is the bringing together chemically of monomers to form a polymer. Physically, polymerization converts the monomer, usually a liquid or a gas, into a rubber, plastic or fibre, depending on the chemical nature of the monomer.
For simplicity, the production of styrene butadiene rubber (SBR), which is the major general purpose synthetic rubber accounting for around 37% of world solid synthetic rubber capacity, will be illustrated. SBR is made from two monomers – styrene, a liquid, and butadiene, a gas. The majority of monomers are derived from oil. Styrene is generally made from ethyl benzene. Although ethyl benzene can be extracted from petroleum ‘streams’ it can also be synthesised from ethylene and benzene. Butadiene can be obtained in many ways from the refinery streams. These streams may be either naturally occurring refinery gases or gases obtained by ‘cracking’, i.e. breaking up larger molecules by heat, usually in the presence of a catalyst.
The polymerization of styrene and butadiene is also conducted in the presence of a catalyst. Polymerization can be carried out by the traditional method, which is dispersion of monomers in water as an emulsion, or in solution in an organic solvent. Any monomers which are not converted into the polymer are recovered, whilst the polymer in a latex form is coagulated into crumb, screened, washed and filtered. The crumb is dried in a hot air drier, after which the dry rubber is baled and wrapped into polythene bags for despatch.